时间: 2025-03-03 09:13:21
来源: UCT
点击率: 185 次
摘要:近年来,冷喷涂工艺越来越多地用于金属部件的增材制造,被称为冷喷涂增材制造 (CSAM)。与基于熔融的增材制造工艺不同,CSAM 是在固态下实现的,具有一些优势,例如不存在严重的氧化或相组成变化。目前,CSAM 的主要限制是喷涂态沉积物普遍较低的延展性。在本文中,我们以铜作为模型材料,展示了一种克服这一限制的方法。重要的是,在不牺牲机械强度的情况下,实现了喷涂态沉积物的高延展性。此外,我们表明,在没有任何后热处理的情况下,CSAM 铜的性能与块状非增材制造铜相当。
关键词:冷喷涂;铜;高延展性;增材制造
近来,冷喷涂技术 (CS) 正逐渐被认为是 一种新型增材制造 (AM) 技术。在冷喷涂工艺中, 微米级的粉末颗粒在推进气体的作用下加速, 推进气体通过拉瓦尔喷嘴供给。然后,颗粒以超音速撞击到芯轴/基材上,并发生广泛的塑性变形,与底层材料形成牢固的结合 [1–3]。冷喷涂具有生产时间短、工艺经济性好、几乎无限的零件尺寸能力以及局部沉积的灵活性。鉴于这些,CS工艺实际上提供了独特的优势与增材制造技术相比,热能是 主要的沉积原理(选择性激光熔化、电子束熔化、激光工程净成形和激光金属沉积)[4,5]。此外,由于CSAM是在固态下完成的,因此金属零件的生产没有严重的氧化或相变 [6, 7],重要的是,CS 更适合于高反射率金属(如铜)的增材制造,而这些金属 使用激光辅助增材制造工艺处理时存在问题 [8]。
冷喷涂工艺现在是一种成熟的技术, 用于各个行业的金属沉积。它已被用于生产保护性 或性能增强涂层,以及接近*终形状的零件 [9]。除此之外,CS 也已被证明是一种经济高效的工艺,用于修复和恢复损坏的航空航天部件(在 [10] 中,修复使用CS修复海鹰直升机模块的案例,从而节省了高达新组件制造成本的 35-50%)。 目前,冷喷涂工艺的主要限制是沉积物极低的延展性,这是由于粉末颗粒的严重塑性变形以及相关的冷作硬化现象引起的。为了恢复延展性,CSAM 材料 通常要经过热处理以诱导再结晶 和固结 [11]。这种在喷涂态下具有高机械强度但几乎为零的延展性,以及通过后热处理提高延展性的方法,已被多位研究人员报道。例如,Meng 等人 [12] 观察到冷喷涂304不锈钢的延伸率低于1%,经过热处理后提高了5倍。对于 Inconel 718,观察到喷涂态材料的延伸率仅为0.5%,退火后增加了8-10倍[13–15]。Yu 等人(2019) 也观察到Cu 具有高机械强度和较差的延展性,几乎没有延伸率,经过热处理后,延展性再次得到改善 [16]。Yin 等人 (2018) 报道,冷喷涂Cu在喷涂态下的延伸率约为 2.5%,在 500 °C 下退火 4 小时后提高了 7.6% [17]。 本研究展示了一种克服该问题的方法。我们的Cu沉积物在喷涂态下表现出高延展性,无需任何热处理。重要的是,这在没有 任何显著的机械强度折衷的情况下实现的,并且使用更便宜的氮气作为工艺气体(不需要氦气)。在本文中, 介绍了粉末粒度和工艺参数对微观结构和力学性能的影响,并将我们的 CSAM Cu 在喷涂态下的性能与块状 Cu 进行了比较。
图 1. 使用的 (a) 细铜粉和 (b) 粗铜粉的粒度分布。
表 1:沉积工艺参数
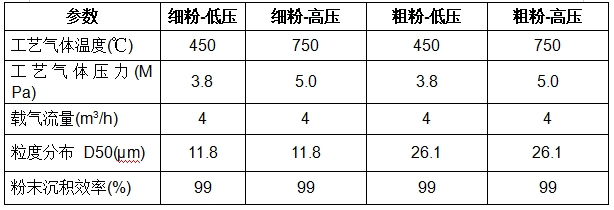
使用两种具有不同粒度分布的高纯度 Cu粉末(99.95%,Impact Innovations GmbH)来验证已发现的原理(图 1)。雾化粉末具有球形形态,图 22 显示了细粉的形貌,其 D10 = 6.2 μm,D50 = 11.8 μm,D90 = 17.8 μm,粗粉的 D10 = 18.9 μm,D50 = 26.1 μm,D90 = 40 μm。 为了帮助理解其基本原理, 通过 CSM EVOLUTION 冷喷涂仪(Tecnar Automation Inc.,加拿大)测量的飞行中粉末颗粒的速度,该设备配备了连续二极管激光源,用于照亮颗粒羽流(790 nm 波长, 3.3 W 功率,70 mrad 发散角)。 使用了具有中央喷射系统的ISS5/8高压枪和OUT1喷嘴(膨胀比5 .6)进行定位。氮气用作推进剂和原料载体气体。结合两种原料粉末(细粉 、粗粉 )和两组建议的工艺参数(低- 低压 、高- 高压 ,表1),准备了四个样本集。LP和HP的参数值是在初步的内部研究中获得的。对于所有四个沉积实验,使用了500mm/s的枪速、30mm的距离和1mm的步长。沉积参数矩阵见表1。对于每组 ,使用尺寸为70×70mm2的两块铝板作为基底沉积5-6mm厚的铜涂层 。沉积后,移除铝板以获得自由站立的铜涂层。未进行额外的热处理。为了帮助理解基本原理,使用配备连续二极管激光源的CSM进化冷喷射仪(Tecnar Automation Inc.,加拿大)测量了粉体颗粒在飞行过程中的速度 ,以照亮颗粒羽流(波长790nm ,功率3.3W,发散角70mrad)。 使用标准程序从沉积物中制备金相样品, 并使用1微米金刚石研磨膏进行*终抛光。使用EVO MA分析样品横截面15扫描电子显微镜(Carl Zeiss,德国)。通过使用FEG/SEM Zeiss Ultra Plus(Carl Zeiss,德国)进行高级电子背散射衍射 (EBSD) 映射,扩展了微观结构分析,该设备配备了 HKL Nordlys EBSD 探测器(Oxford Instruments,英国)。EBSD 数据集是在 20 kV 的加速电压下采集的,在高/电流模式下使用Aztech软件(Oxford Instruments,英国)时,孔径为120微米。采集步长为200纳米,相机合并经过调整,以实现可靠的模式识别(在本例中为 4 × 4)。 样品的致密性通过使用氦气泄漏检测器(Qualytest HTL 260,Pfeiffer Vacuum GmbH,Asslar,德国)在德国 Forschungszentrum Jülich 的 IEK-1 中进行气密性测试来评估。在沉积物的一侧保持 He 的流动,同时在其另一侧抽取真空。记录通过样品泄漏的 He 的量。 对于机械性能测试,选择了拉伸测试和硬度测量。对于前者,从独立式Cu 中电火花线切割出扁平试样(长度为60毫米),并根据 ENISO 6892–1 标准使用传统拉伸试验机进行测试,不同之处在于建议的机械引伸计被虚拟数字图像相关 (DIC) 引伸计取代。此前已评估该装置是进行材料表征的有效方法 [18, 19],并且表明非接触式引伸计产生的结果与机械引伸计获得的结果完全相当。使用虚拟引伸计的另一个优点是,*大限度地减少了由于引伸计刀具刮擦样品表面而导致裂纹萌生的可能性。以0.4毫米/分钟的恒定速率施加拉伸载荷,直至断裂,并记录材料的应力响应。使用Q10A+(Qness,奥地利)通过维氏法测量沉积物的硬度。考虑到晶粒尺寸和微观结构特征,所有样品均选择300gf 的载荷 (HV0.3)。测量按照 ISO6507–1标准进行(压痕间距至少为压痕尺寸的3倍)。使用20个压痕来计算每个样品的平均值。对于细粉和粗粉,使用双尾非配对t检验来确定在低压 (LP) 和高压 (HP) 下生产的沉积物的硬度之间的统计显着性。使用的显着性水平为 *p = 0.01。 样品的热conductivity λ值是根据热扩散系数a、密度P和比热容cp的 测量结果,按照公式laλ=a×P×cp计算得出。热扩散系数的测量采用激 光闪蒸法,在真空条件下使用LFA 1000测试仪(德国林赛公司)进行。为了确保吸收均匀,吸收为了使激光脉冲的吸收均匀且表面的辐射特性相等,将10x10x2mm3样品涂上一层薄薄的石墨。对于所有样品,在每个温度下(从20到800 'C)进行五次测量。样品的密度p使用阿基米德方法(将样品浸入水中)测量,其各自的温度依赖性是基于纯块状铜的密度-温度依赖性计算的。对于计算,使用了纯铜的热容C。 将通过各种方法获得的性能与块状铜材料进行比较。为了避免混入潜在的第二影响并保持完全的相互可比性,Cu块体是与用于雾化此处使用的两种粉末相同的材料。图 2. 所用细铜粉和粗铜粉的球形形貌。
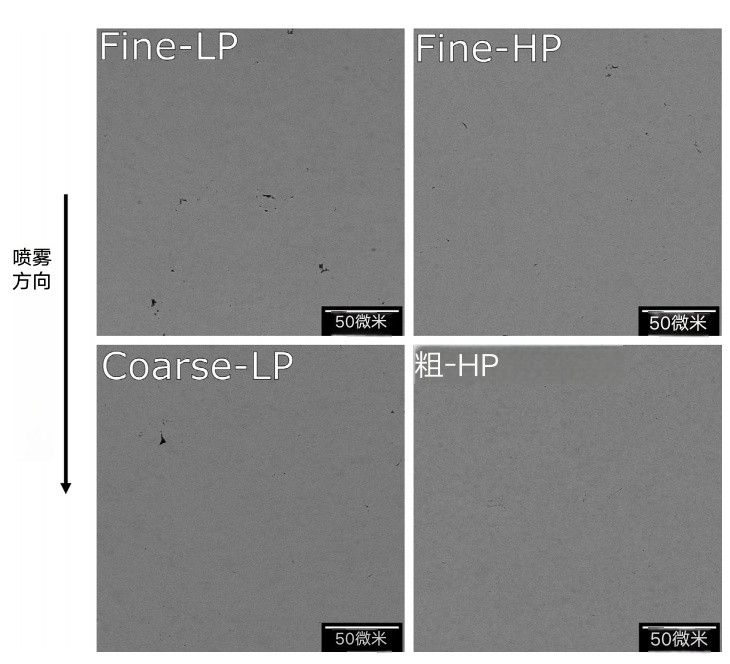
图 3. 四种 CSAM 铜沉积物的致密微观结构。
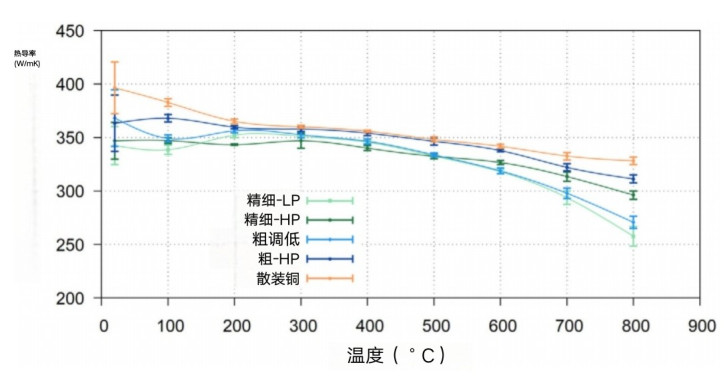
图 4. 四种 CSAM 铜沉积物和块状铜的导热率。
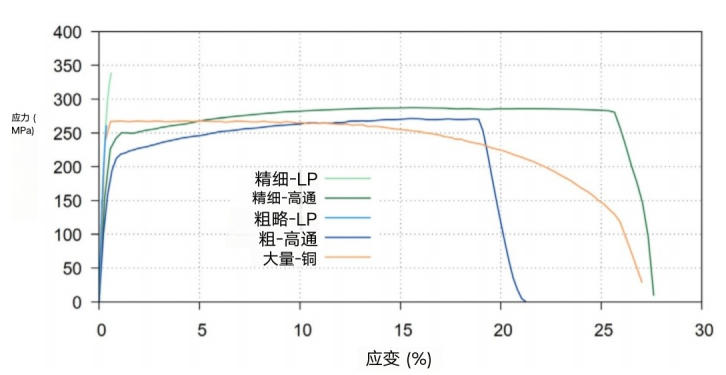
图 5. 应力-应变曲线显示了在高工艺参数下沉积的冷喷涂铜具有高强度和延展性,与块状铜的性能完全相当。
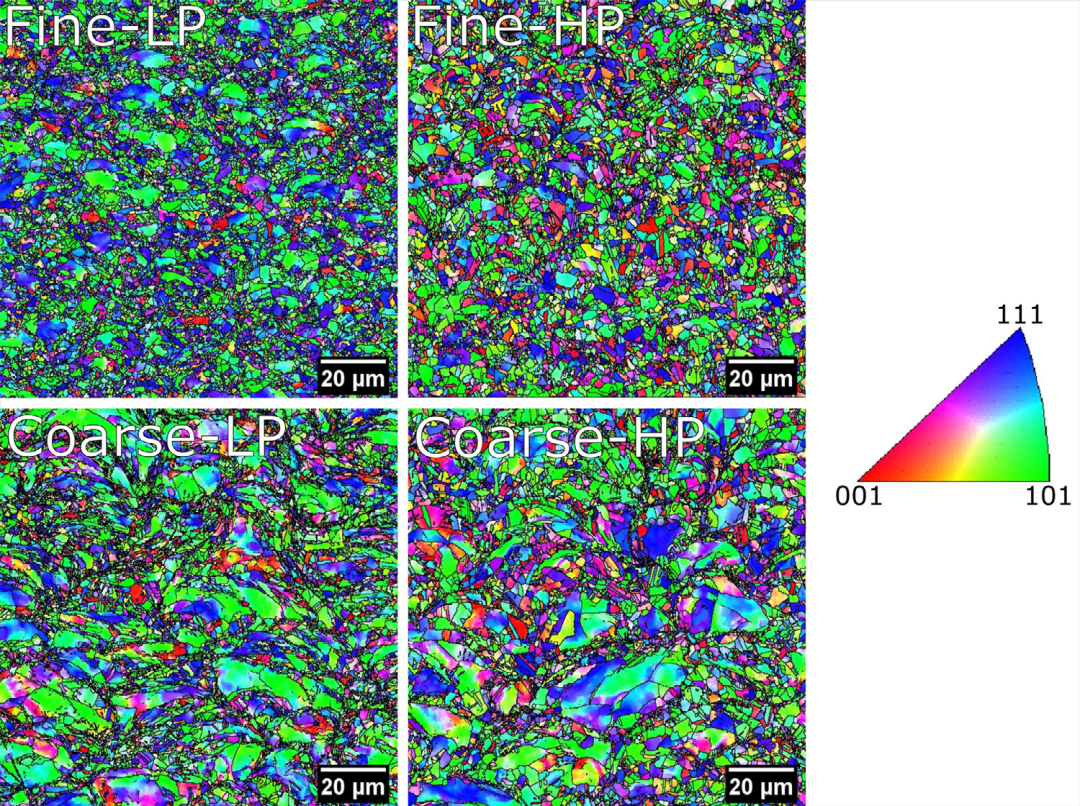
图 6. 冷喷涂铜沉积物微观结构的EBSD IPF 图,显示双峰晶粒分布。
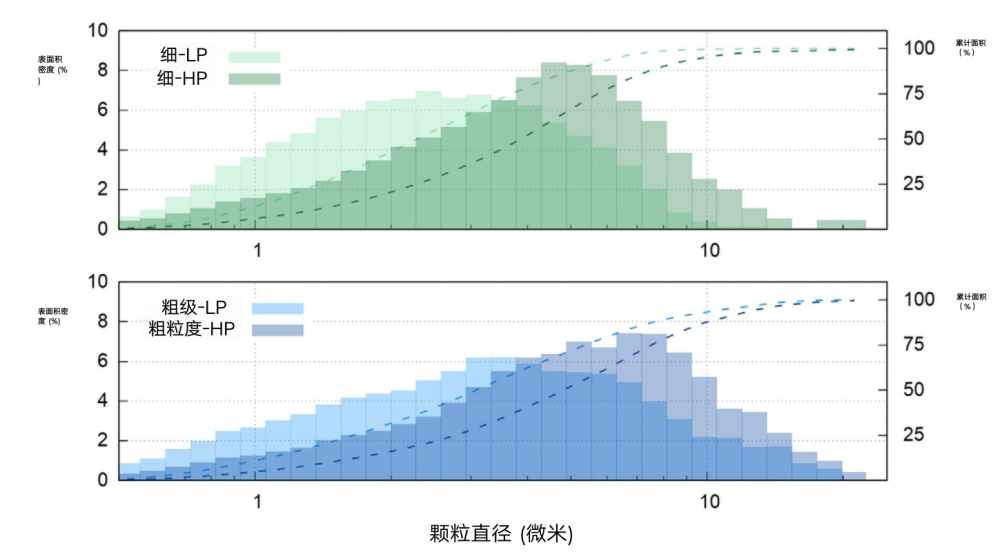
图 7. CSAM Cu 沉积物中的面积晶粒尺寸分布。
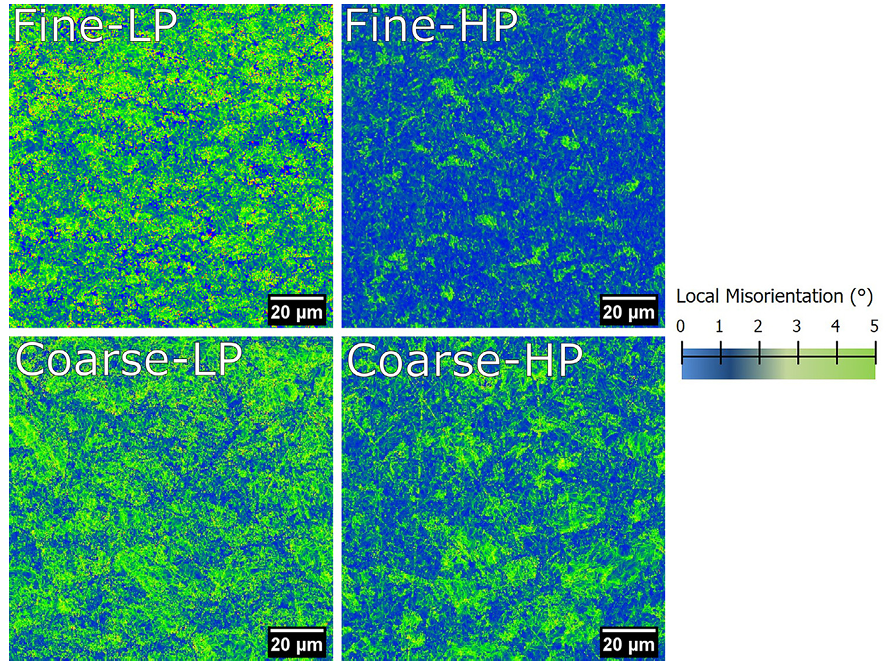
图 8. 冷喷涂铜的局部晶粒取向差图,显示了局部塑性应变的量。
图33中的SEM BSE 显微照片显示,在低参数和高参数下,由两种粉末沉积的材料都具有非常致密的微观结构。事实上,通过阿基米德浸没法测定的Cu沉积物的密度(表 2)对应于低于1.5%的孔隙率,即与块状冶金Cu相当的值。为了进一步评估密度,使用 He 泄漏检测对致密的Cu沉积物进行了气密性测试。在所有沉积物中,观察到小于1×10−7mbar•l/s 的He流量。根据 [20, 21],低于1 ×10−7mbar •l/s 的值被认为是非常密封的系统。换句话说,该测试证实了冷喷涂沉积物非常致密,并且Cu沉积物中有限的孔隙率不是相互连接的。 如果与其他增材制造工艺生产的铜进行比较,所获得的密度值会更加突出。例如,Lykov等人(2016 年)在通过选择性激光熔化工艺生产的铜中实现了88.1% 的密度 [22],而 Kumar等人(2019 年)在通过粘结剂喷射增材制造生产的烧结和 HIP铜中测量了77% 到97% 的密度 [23]。 如图 4 所示,记录了Cu沉积物的导热率,温度范围为20–800 °C。可以观察到,所有样品的导热率与块状Cu对应物相当,间接证实了沉积物的质量。略微更好的HP沉积物值(在较高温度下更为明显)可能源于它们略微更好的密度和不同的微观结构拓扑(在第3.2.1节中讨论)。还可以观察到,粗粉沉积物表现出比细粉沉积物略高的导热率,这在两种工艺参数下都是相似的趋势。这可能再次是由特定的微观结构拓扑引起的。对于所有样品,导热率随着温度升高而降低。在金属中,这是一种众所周知的现象,因为它们的导热率主要取决于电子的流动,而电子的流动受到升高温度下晶格振动的阻碍 [24, 25]。 图5显示了具有代表性的应力-应变曲线。这些结果表明,在低压 (LP) 下,两种冷喷涂沉积物都表现出高抗拉强度,但延展性非常低。这些特性是沉积态 CSAM材料的典型特征,并且是粉末颗粒塑性变形过程中极端加工硬化的结果。改变游戏规则的结果是在高压 (HP) 下沉积的Cu样品的曲线。这些曲线的特点是高抗拉强度和高延展性,两者都与块状(即非增材制造)对应物完全相当。开发一种同时具有高强度和高延展性的增材制造材料一直是一项具有挑战性的任务,特别是自从强度和延展性通常是相互排斥的。据我们所知,以前没有报道过冷喷涂铜在喷涂状态下能取得这样的结果。 拉伸测试数据进一步表明,使用较细粉末在两种工艺参数下喷涂的铜涂层,与使用较粗原料粉末喷涂的铜涂层相比,显示出更高的强度。然而,这种影响不如工艺参数的影响显著。 将晶粒从粗晶细化到超细晶,再到纳米级晶粒,是强化金属材料的一种众所周知的方法[26, 27]。这种方法的代价通常是延展性较差,因为储存位错的能力有限,导致在机械加载过程中早期发生应变局部化。为了克服这个问题,制造双峰晶粒尺寸的微观结构已被证明是一种在超细晶材料中提高延展性的策略,但会略微牺牲拉伸强度。在具有这种双峰晶粒尺寸分布的材料中,超细晶提供高强度,而粗晶则作为位错存储的“阱”,从而提高延展性[28-31]。拉伸测试数据表明,在高功率(HP)条件下,铜涂层可能具有这种双峰微观结构,使其具有高强度和延展性。为了研究这一假设,并检测潜在的微观结构再结晶,我们获取了所有四个冷喷涂增材制造(CSAM)涂层的电子背散射衍射(EBSD)反极图(IPF)和局部晶粒取向差(KAM)图。 图 66 中所示的反极图(IPF)清楚地显示了一种特定的微观结构,其中位于原始铜颗粒中心的粗晶区域被沿颗粒边缘的几微米大小的超细晶的连续网络所包围。细粉-低功率(Fine-LP,颗粒速度 688 米/秒)和细粉-高功率(Fine-HP,颗粒速度 813 米/秒)涂层的反极图显示,在两种工艺参数下都形成了清晰可见的双峰结构。然而,在低功率(LP)条件下,粗晶和细晶的空间拓扑分布并不均匀,一些区域只显示细晶,并且超细晶网络的分布也进一步不均匀。与低功率(LP)条件相反,细粉-高功率(Fine-HP)涂层的微观结构显示出粗晶和细晶均匀的空间拓扑分布,其中粗晶区域有规则地被相互连接的超细晶网络所环绕。正如其他研究(例如,Zhang 等人对 304L 不锈钢的研究 [32])所发现的,空间拓扑分布(这里讨论的是我们的涂层)是在高功率(HP)条件下同时实现高延展性和高强度的另一个主要因素。在低功率(LP)和高功率(HP)条件下,粗铜粉末涂层的微观结构也观察到类似的行为:粗粉-低功率(Coarse-LP,颗粒速度591米/秒)的微观结构显示出分布不均匀的细长的大晶粒,以及不规则且相对较厚的超细晶网络,而粗粉-高功率(Coarse-HP,颗粒速度662米/秒)则显示出更均匀分布的粗晶区域,这些区域被相对较薄的超细晶壁所环绕。在所有涂层中,微观结构中观察到的细长粗晶的出现可能是由于粉末颗粒撞击期间的射流现象造成的,正如 Borchers 等人 [33] 和 Rahmati 等人 [34] 所报告的那样。 从电子背散射衍射(EBSD)结果可以清楚地看出,所有四个涂层都表现出双峰结构,但它们的细晶和粗晶比例不同。为了量化这种差异,我们使用EBSD反极图(IPF)来计算每个涂层内的面积加权晶粒尺寸分布(图7)。直方图清楚地表明,工艺参数(低功率LP与高功率HP)对晶粒尺寸分布产生显著影响。对于两种类型的原料粉末,在高功率HP下喷涂的涂层显示出更大比例的较大晶粒。这种转变是由前文讨论的晶粒再结晶引发的,并产生一种由细晶和粗晶组成的微观结构。就绝对值而言,细粉和粗粉的中值晶粒尺寸分别从2.3微米变为3.9微米,以及从 3.1微米变为4.8微米。此外,与工艺参数的影响不同,在低功率LP和高功率HP 下,两种粉末之间没有显著差异。 为了进一步了解微观结构的形成,我们从反极图(IPF)中计算了局部晶粒取向差(KAM)图,揭示了涂层中的塑性应变程度(图 8)。结果表明,在低功率(LP)下喷涂的两种涂层都表现出粗晶内部以及晶界处的高度应变。还可以观察到,未指数化区域(主要限于颗粒边界和粗晶-细晶界面区域)的比例在细粉-低功率(Fine-LP)中更高,表明要么是具有高位错密度的高度变形区域,要么是小于电子背散射衍射(EBSD)分辨率限制的非常小的纳米晶特征。与低功率(LP)的图相比,两种高功率(HP)涂层的取向差图显示出应变较小的区域,并且几乎没有未指数化的区域。 总而言之,电子背散射衍射 (EBSD) 结果表明,虽然塑性应变仍然存在,但热软化和再结晶在粒子极高冲击速度造成的剪切应变中占主导地位。文献中也有报道,对于铜而言,超过600米/秒的颗粒速度足以将局部温度升高到接近熔点,即足以在高度应变的材料中发生动态再结晶 [33-35]。在本研究中,在低功率 (LP) 和高功率 (HP) 下获得的颗粒速度足以触发两种粉末的这一过程。 在之前的研究{例如,[33]}中,有人提出在高应变速率变形的动态再结晶过程中,微观结构的演变分为五个阶段:(i) 位错的随机分布,(ii) 通过形成细长的位错胞进行动态回复,(iii) 细长的位错胞排列形成细长的亚晶粒,(iv) 细长的亚晶粒的分解,以及 (v) 形成具有小等轴晶粒的再结晶微观结构。正如Borchers 等人 (2003) 和Schmidt 等人 (2006) 所报告的那样,更高的颗粒速度会产生更高的局部温度升高,从而为微观结构的演变提供更多时间 [33, 36]。 本研究的结果表明,在低功率(LP)条件下,高温条件存在的时间不足,因此,再结晶无法充分发展。相反,微观结构的发展在早期阶段停止,因此,形成了观察到的高度应变和非均质的双峰微观结构。这影响了冷喷涂增材制造(CSAM)铜涂层的力学性能,表现出高强度但非常低的延展性。与此相反,在高功率(HP)下,两种粉末的更高颗粒速度会诱导更高的温度,从而促进动态再结晶并刺激完全发展的具有松弛晶粒的双峰微观结构。结果进一步表明,需要均匀且松弛的双峰微观结构,其中粗晶区域被超细晶的连续网络所环绕,才能获得同时实现高强度和高延展性的协同效应。在本研究中,对于在高功率(HP)下喷涂的两种粉末都观察到了这一点。Jakupi 等人 (2015) [35] 此前也报道了冷喷涂铜中的双峰微观结构。然而,那里展示的双峰结构在粗晶区域和超细晶网络的空间拓扑分布中表现出异质性,因此,观察到的高强度伴随着非常低的延展性,这与我们在低功率(LP)下的结果相似。 图9展示了粉末粒度和工艺参数对冷喷涂增材制造(CSAM)铜涂层硬度的影响。硬度趋势与拉伸强度行为趋势一致(图5),即细粉涂层由于其更细的晶粒结构(如图6所示)而显示出更高的硬度值。细晶微观结构包含高密度的晶界,这些晶界充当位错运动的障碍,导致压痕期间位错在靠近晶界的区域堆积。因此,需要更高的应力才能使位错通过这些堆积,从而导致硬度增加[37]。 然而,在所使用的工艺参数下,细粉和粗粉涂层的硬度值差异并不是非常显著。与此相反,工艺参数的影响得到了很好的体现。通过双尾t检验进行的统计分析表明,在低功率(LP)和高功率(HP)下沉积的样品的硬度平均值之间存在显著差异(p<0.01)。显然,正如第3.2.1节中所讨论的那样,在低功率(LP)下,剪切应变在再结晶中占主导地位,而在高功率(HP)下,获得了完全再结晶和松弛的微观结构。因此,两种高功率(HP)涂层的硬度均降低。非常低的标准偏差表明,所有四个冷喷涂增材制造(CSAM)铜涂层在宏观性能方面都非常均匀。*后,冷喷涂铜涂层的硬度与块体铜相当。 使用球形粉末、高压枪和氮气作为工艺气体,制造出了纯铜的冷喷涂增材制造(CSAM)涂层。研究了工艺参数和粉末粒度的影响。从结果中可以得出以下结论: 几乎无孔的铜涂层(密度为 8.79–8.84 g/cm3,完全抑制氦气泄漏)可以通过冷喷涂增材制造(CSAM)生产,其热导率高达 368 W/m•K,与原始喷涂状态下的块体铜(396 W/m•K)相当。 在没有任何二次加工(如热处理)的情况下,无论使用何种铜粉,在高喷涂参数下,涂层都可以实现同时具有高强度和高延展性。这得益于双峰微观结构的有利拓扑结构,该结构由粗晶组成,这些粗晶被沿单个颗粒边缘的细晶网络所包围。 工艺气体参数(温度和压力)对力学性能的影响比所用原料的平均粒径更为显著。在冷喷涂增材制造(CSAM)铜中实现了286MPa 的极限抗拉强度和24%的延展性的组合。 在我们的工作中开发的冷喷涂增材制造(CSAM)铜涂层的热力学性能与采用非增材冶金方法生产的块体铜完全相当。考虑到高沉积效率(99%)和高沉积速率,本文说明了该方法在各个工业领域中具有巨大的应用潜力,无论是在高要求的应用中还是在批量生产中。注:此文献由deepseek翻译,如有不妥之处,欢迎指正!